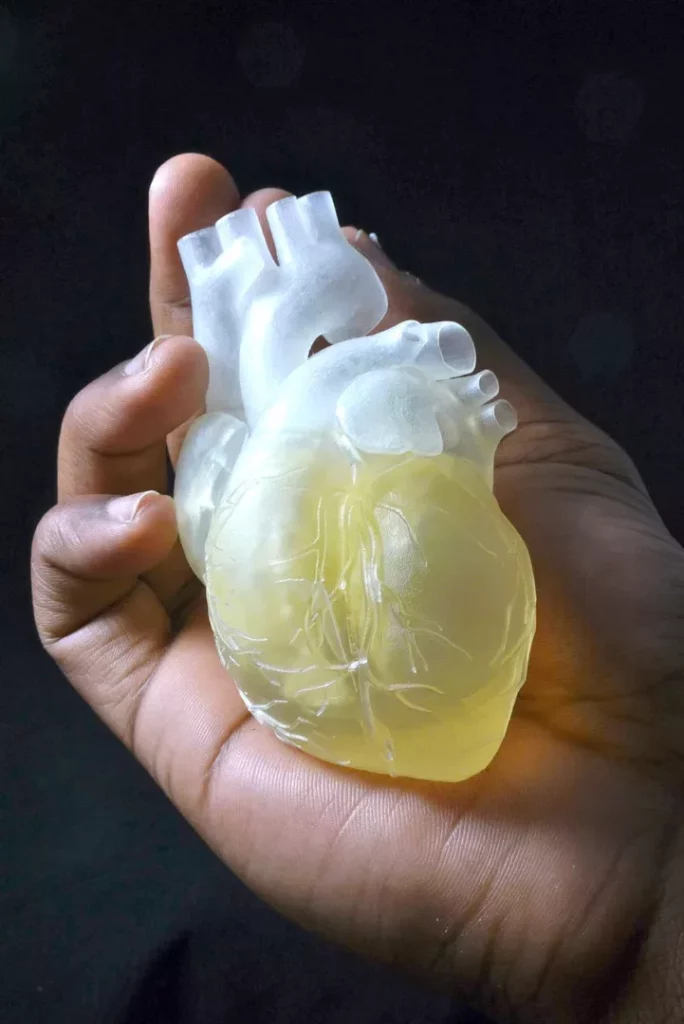
For applications requiring complex geometries or lightweight designs, 3D printing’s additive manufacturing process offers unparalleled advantages. When required, we can also combine technologies to find the complete solution to a customer’s manufacturing needs. Here are a few examples:
Rapid Prototyping
Rapid prototyping is one of the best applications of 3D printing for industry. 3D printing produces functional prototypes, meaning the full design is 3D printed in working mode, usually without need for assembly.
Best of all, since the process starts with a Computer-Aided Design (CAD) file, changes can be made quickly and easily right on your computer, eliminating the time and expense of creating a new mold.
3D printing with durable materials like ABS enables you to test parts directly in their intended work environment. Once the design is finalized, the part can be seamlessly transitioned to its final material, such as stainless steel or aluminum.
Microfabrication
With our high-resolution 3D printers and extensive experience working in the micro digital fabrication space, Potomac can manufacture parts on very small spatial scales. Miniaturization in all industries is on the rise, especially for new medical devices, microelectronics, sensors, microfluidic devices, consumer products, and security systems.
Fixturing
At Potomac, fixturing plays a crucial role in successfully completing jobs, whether it’s laser micromachining, micro CNC machining, or other precision processes. Many of the parts we produce are extremely small and difficult to hold, requiring us to design and create custom fixtures.
3D printing often enables design consolidation by allowing the creation of complex geometries in a single process, significantly reducing part counts and lowering costs. Additionally, it provides the flexibility to quickly modify fixture designs as customer parts evolve. This fast and efficient fixture production eliminates the need to store outdated fixtures, saving both time and space.
For a recent laser micromachining project, we produced medical devices designed to deliver cancer drugs to targeted areas of the body. The parts were thinner than a human hair and required precise stabilization during machining. Using 3D printing, we created a custom fixture that securely held the parts in place, enabling us to laser micromachine them with exceptional accuracy and tight tolerances.
Medical Devices
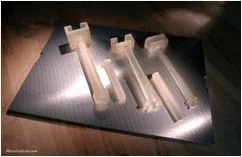
Potomac has a long history of partnering with medical device companies to advance the industry through next-generation manufacturing techniques. In our early days, we leveraged emerging laser micromachining technologies to produce some of the first coronary stents and helped manufacture the first glucose sensor for the insulin pump. By incorporating 3D printing into our fabrication toolkit, Potomac continues to drive innovation and support cutting-edge medical device development.
Example: CyroPop
Developed by Momo Scientific, a Johns Hopkins University spin-off, the CryoPop is a low-cost medical device that uses a cryogenic process to treat cervical pre-cancerous lesions. With the easy availability of CO2 cartridges from the soda industry around the world, costs are low, and many lives can be saved.
Potomac was able to provide the high-resolution precision required to meet the critical design parameters, ensuring the device’s effectiveness and reliability.