Potomac – UMBC Collaboration to develop novel manufacturing techniques for microfluidic devices shows early, promising results.
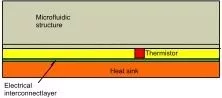
Microfluidics is the science of designing, manufacturing, and developing devices and processes that deal with extremely small volumes of fluid for many types of applications, including sensing, drug discovery, alternative energy, and point-of-care diagnostics. Testing and analysis processes, that would normally be performed in a lab, have now been miniaturized and can be conducted on a single chip in order to enhance efficiency and mobility, as well as, reducing sample and reagent volumes. Recently, Potomac and its partners at UMBC and Potomac Mesosystems have embarked on several projects to develop novel microfluidic manufacturing technologies.
Surface mount thermistors for heating and sensing
In our first study, we’re investigating the use of submillimeter thermistors as combined heat sources and temperature sensors. We’re using the smallest negative temperature coefficient thermistors with a footprint of 0.3 mm x 0.6 mm (0201 size).
When thermistors are used for temperature sensing, great care is normally taken to avoid self heating of the thermistors by the sensing current. In our case, we’re purposely self-heating the thermistor and monitoring its resistance to infer its temperature.This gives us a tiny heat source with an easily measured temperature that can be placed in close proximity to a microfluidic channel.
Because of the complex heat flow patterns in a typical microfluidic structure, it is very helpful to use a 3D modeling program to estimate temperature distributions, required power input, cooling time constants and other important parameters. The sketches to the left show a cross-section of a simple thermistor heater layout and the results of a Comsol model of the corresponding temperature distribution. We are now constructing and modeling several single-thermistor configurations.
A “hot thermistor” flow sensor for microfluidics
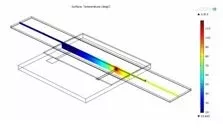
A large variety of microfluidic flow sensors based on micromachined heaters and RTD’s have been reported in the literature. Hot wire flow sensors – the analog of hot wire anemometers — are among the simplest of these, since they can be fabricated with a single heater with a well-defined relationship between resistance and temperature. Implementation requires only a resistive heater fabricated from a very narrow and thin conductor that is placed near a microfluidic flow stream. The heater is positioned near a heated with a drive current, and its temperature isinfluenced by the cooling effect of the nearby fluid flow. Higher flow provides more cooling and lower heater temperatures. Calibration of temperature (i.e. resistance) vs. flow results in a simple flow monitor. Heater dimensions are typically such that fabrication is by photolithographic patterning of a metal film of submicron thickness. For good sensitivity, the heater should have a high thermal coefficient of resistivity.
We’ve recently shown that a small, surface-mount NTC thermistor can be substituted for the patterned thin metal film, with significant implications for reduction of process steps and costs associated with fabrication, and increased speed and simplicity of rapid prototyping of integrated flow sensors. The very high temperature coefficient of thermistors provides good flow sensitivity, and use of surface mount electronic assembly techniques simplify fabrication.
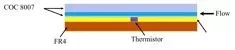
In work carried out in the Potomac laboratory, Amir Harandi, a Ph.D. student at UMBC, fabricated a hot thermistor flow sensor like that shown at the right. The microfluidic channel had a cross-section of 300 microns x 600 microns, and a 2Kohm NTC thermistor with a 0201 package size was used in the experiments. Experimental results are summarized below, and demonstrate the relatively large electrical output variation produced by flow rates between 0 and 50 ul/min.
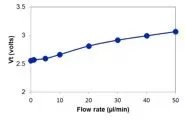
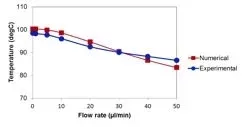
Availability of microfabrication tools at Potomac, such as lasers, micromills, plastics bonding, hot embossing, dispensing, and pick-and-place equipment, allows fabrication of of microfluidic prototypes that incorporate electronics in just a few hours.
For over 30 years, Potomac Photonics has been a leader in microfabrication and small hole drilling. Potomac’s contract services span prototyping to production, helping clients develop miniature products and bring them to market. Using cutting-edge manufacturing technology, Potomac has been recognized by both commercial and government agencies for innovation in areas such as medical device, electronics, aerospace, and automotive manufacturing. Potomac’s high-tech facility, located at bwtech@UMBC Research and Technology Park , is ISO 9001 and ISO 13485 certified. Visit the website at www.potomac-laser.com