CAD-based laser micromachining allows designers to make quick, economical design changes
July 23, 2015; Baltimore, MD: Using CAD-based Digital Fabrication tools, Potomac Photonics is able to provide designers with a quick, economical method to test and change designs. A research team at the University of Texas, MD Anderson Cancer Center in Houston recently implemented the Potomac process to study the machinery of mucus secretion in asthma.
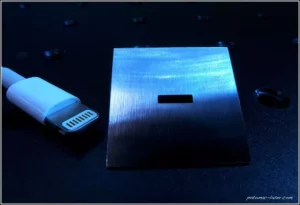
Dr. Michael Tuvim, Director of Laboratory Research, in the Department of Pulmonary Medicine explains that the group’s mucus secretion studies are aimed at developing an assay in order to record mucus eruption in real time, which does not currently exist. Excessive mucus production that cannot be cleared by normal ciliary action blocks airflow. In fact, the cause of death from asthma is actually suffocation.
Using fluorescent detection technology with mice trachea that have been pre-stained with an orange fluorescent dye, the researchers can stimulate baseline secretion, depleting the stores of mucus production and consequently stopping explosive secretion. In their initial experiments, Dr. Tuvim’s team built a flow chamber to house unfurled and flattened trachea explants. They then prepared and mounted the trachea samples on glass microscope slides. He says, “The system will allow us to mimic physiological conditions and visualize the changes in secretion (recorded and measured as changes in fluorescence) under the microscope in real time.”
Potomac provided a glass coverslip containing a 1.5 x 1.5 mm window for the light exposure. Explains Dr. Tuvim, “Creating the small size of the window was prohibitive for traditional glass cutting methods. Potomac Photonics was one of the few companies that could meet our small size requirement and not damage the glass.”
However, as is common in the research phase of scientific work, the glass slides didn’t provide the optimal result for the team. The glass slides were too fragile for the process to work and so a return to the proverbial drawing board was needed.
“Potomac worked with Dr. Tuvim,” says Potomac President and CEO Mike Adelstein, “to find a material that would be more robust for his experiment. Because we have a wide range of material processing capabilities we were able to provide a solution in thin stainless steel.”
The design could also be easily modified because CAD-driven digital fabrication tools such as laser micromachining are flexible. Without the need for masks, changes are immediately drawn in computer software and translated directly by the machines. Time and cost are greatly reduced, giving researchers and designers an opportunity to test various models.
As inventor Thomas Edison once pointed out, “I have not failed. I’ve just found 10,000 ways that won’t work.” Progress in science and engineering are furthered by a process of trying and testing and trying again. When a designer can quickly and easily test new designs, it speeds up the entire invention and product development cycle. Companies can get products to market quicker and design optimization ensures greater success in the marketplace. For researchers such as Dr. Tuvim’s group, it can more importantly, save lives.
About Potomac Photonics
For over 30 years, Potomac Photonics has been a leader in microfabrication, laser micromachining and small hole drilling. Potomac’s contract services span prototyping to production, helping clients develop miniature products and bring them to market. Using cutting-edge manufacturing technology, Potomac has been recognized by both commercial and government agencies for innovation in areas such as medical device, electronics, aerospace, and automotive manufacturing. Potomac’s high-tech facility, located at BWTech@UMBC Research and Technology Park, is ISO 9001 and ISO 13485 certified. Visit the website at www.potomac-laser.com