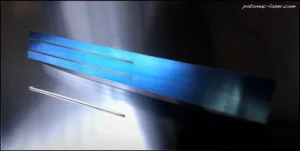
Anyone who has found themselves without the power cord for their laptop, iPad or smart phone knows the frustration of living in a “connected” world. Energy-harvesting is one of the research areas that would cut the cord, so to speak, to our electricity dependence. There is energy all around us, but the challenge is to capture and store it for use when we need to be “plugged in”.
Potomac has been laser micromachining new types of devices to help UMBC Mechanical Engineering Department Assistant Professor Soobum Lee realize his dream of charging your cell phone while you walk. Dr. Lee’s research centers on a popular topic of harvesting energy from vibrations. He explains that waste vibration energy is all around us in our environment. Autos, planes and even appliances in our kitchen generate vibrations that are not utilized by the machine.
The UMBC project laminates a piezoelectric energy-harvesting skin (EHS) onto a vibrating substrate and then stores the converted energy in a small battery. Dr. Lee points out that vibrations in the real world are not fixed but rather occur randomly. In order to respond to this fluctuation, the researchers are prototyping substrates with sophisticated designs that require high precision structures to capture the random vibrations.
Using tools that were available in the engineering school, the research group could not get the precision structures they needed. Then Professor Lee heard a talk by Potomac President and CEO Mike Adelstein at UMBC. “I realized this was the level of micro-fabrication that would work,” says Dr. Lee. “And it’s an added bonus that we are located so close to the Potomac facility.”
The prototypes that Potomac helped manufacture are helping define the level of response of the device. Simulation work is almost complete and then there will be actual implementation tests. “The beauty of digital fabrication”, elaborates Dr. Lee, “is that we can refine our designs quickly and easily in CAD for Potomac to create new substrates if we feel we need to make any changes as we review results.”
Right now Dr. Lee’s energy harvester can drive small devices such as wireless sensors, but we hope that Potomac’s high precision work on the new designs can help realize his dream of charging your cell phone while you walk!