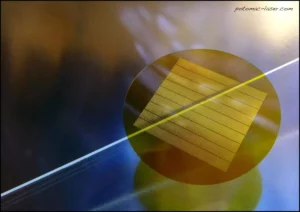
Rapid prototyping is a proven method to move a product from concept to production that has been in engineering practice for decades. Especially with the advent of new digital fabrication technologies such as 3D Printing and laser micromachining, iterative design changes in CAD software yield an optimized product that is ready for market with greater chance of success.
However, unique designs mean that tooling must be changed for each job and when using a contract service bureau that means higher cost due to set up time. To help our customers who need to quickly and economically pre-test prototype ideas, we’ve introduced Potomac Proving Ground. The new design testing service gives engineers and designers in biotech, medical device, microelectronics, microfluidics, and consumer products companies a first step to try an idea by keeping within certain parameters that reduce set up cost.
By analyzing the thousands of parts we have manufactured in diverse industries, the most common design parameters needed in laser micromachining for advanced manufacturing were easy to spot. Our dedicated Potomac Proving Ground laser micromachining workstations ensure both fast set up and processing speeds for high through put, reducing expense and increasing turnaround time.
While Potomac’s custom rapid prototyping service with full range of parameters is always available, as a first cut parts using the Potomac Proving Ground must follow specific Design Rules:
- Overall part size should be less than 40 mm x 40 mm
- Only files in DXF format can be accepted
- DXF drawing should consist only of lines, polylines, circles and arcs. Use of ellipses, elliptical arcs, splines, bezier curves, etc. will cause the file to be rejected. The presence of 3D elements in the drawing will also cause it to be rejected.
- Duplicated or overlapping drawing elements will cause segments to be cut more than once. These will be reported as drawing errors, since they can impact the quality of the part.
- DXF drawing feedback will be summarized for customers in order to expedite corrections
- Submitted designs will be cut exactly as submitted. The cut pattern will not be adjusted to compensate for the laser’s beam width. Kerf width is then:
o For Kapton substrates, the width of the laser cut (kerf width) is approximately 20 microns at the bottom of the cut.
o For stainless steel substrates, the width of the laser cut (kerf width) is approximately 30 micron at the bottom of the cut
- For all materials, the vertical angle of laser-cut edges called taper is typically 10 degrees
- Minimum hole size for all materials is 50 microns in diameter.
- Post processing and pre-shipment inspection will be limited to measurement of outside dimensions and confirmation of slug removal
Once the first round of parts are manufactured using the Potomac Proving Ground and are verified by the customer, designs can be optimized and moved to the prototyping and/or short production run stage. Since at this point many design issues will have already been solved, cost is usually less than when starting without the new pre-prototyping design testing service.
Potomac’s standard service to rapid prototype small parts in a wide range of materials from glass to organic polymers, diamond to metals, and everything in between, is always available. However, for a fast solution to testing a new product idea, Potomac Proving Ground can move a product to market faster and more affordably, which is key in today’s fast paced world.
Details about the Potomac Proving Ground advanced manufacturing design testing service are available on the Potomac website: Proving Ground Page. For consultation, please email [email protected] or call 443-543-5737.