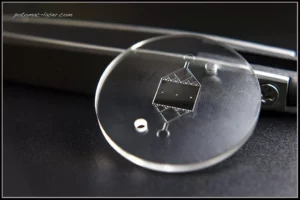
Potomac has many competitive advantages that has made it a leader in the advanced manufacturing industry. We offer the fastest turnaround times, often as quickly as 24-hours; our quality control systems are second to none; and the wide range of technologies on our factory floor always ensure we can choose the right tool for the job.
But perhaps our greatest strength is our commitment to cutting edge research and development. Our forward-thinking Process and Product Technology [PPT] team is a talented team of innovators that drive technological breakthroughs in order to solve our customers’ most complex problems.
Leading the Potomac PPT effort in laser welding, Senior Technical Researcher Natalia Christensen has recently developed a new process to laser weld clear plastics that are between 50 and 200 microns thick. “There are many advantages to the new Potomac laser welding process,” explains Natalia, “which will open new manufacturing options in industries from microfluidics and medical devices to consumer products and aerospace.”
Laser welding clear plastics like COP, COC, PMMA, acrylics, polycarbonates, and polystyrene has several advantages over other bonding methods in specific applications. For example, devices that have been fabricated using thermal bonding cannot be easily integrated into high temperature environments without weakening the bond. In addition to withstanding heat, laser welding can also provide higher bonding strength as the light penetrates deeper, but also the amount and location of the light can be precisely controlled.
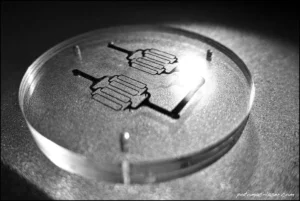
In microfluidic applications, smaller channels require more delicate handling procedures, giving laser welding considerable technical advantage in this application. When channels are smaller than 200 microns wide, excessive pressure can distort the microfluidic pattern which is not a problem when utilizing “non-contact” laser material interaction.
Potomac President and CEO Mike Adelstein points out: “Having a specialized capability like laser welding of clear plastics adds an important technology to our toolbox. We are always developing a wide range of complementary tools so that we can accurately and economically respond to our customers. Joining materials is powerful for many applications as we move from parts to sub-assemblies to finished products in order to provide a complete manufacturing solution.”
Next, Natalia and her PPT team have started R&D to laser weld dissimilar materials such as PMMA and polycarbonate, and to join multiple thin layers simultaneously. We expect the new processes will further Potomac’s ability to lead the industry through powerful technical innovation for advanced micro-fabrication.