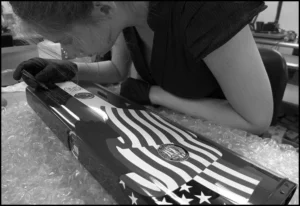
How we helped Fab Lab Baltimore and in the process gained valuable workforce development.
Potomac’s move to the UMBC campus has reaped a number of benefits for Potomac, one of which was most unexpected. The new facility is located about a mile from the Community College of Baltimore County [CCBC] where Fab Lab Baltimore [FLB] is located. Like many Fab Labs in the international MIT network, FLB is continually exploring ways to create a sustainable business model for the lab. Community colleges may provide space and equipment but operating funds are hard to procure.
To involve the local business community in the sustainability dialog, Fab Lab Founder Ken Burch invited Potomac President and CEO Mike Adelstein to be part of a new FLB Advisory Board. Says, Mike Adelstein, “After seeing FLB’s people resources I realized working together was a good fit. We had the full complement of Fab Lab tools including 3D Printing, laser machining and marking, and CNC machining but we didn’t have the staff to work on the larger spatial-scale jobs that come to us through our extensive marketing communications program.”
Ken Burch adds: “We needed to be able to demonstrate to CCBC that FLB could sustain itself so the partnership with Potomac was obvious. What I didn’t expect was that the collaboration with Potomac would give our people new skills and insight that they would bring back to FLB and apply to commercial settings.”
Fab Lab Baltimore has interns from CCBC, UMBC, and also the Maryland Institute and College Art that Potomac hired through FLB. Mike Adelstein of Potomac was impressed that the interns they hired were such quick studies. Demonstrating solid skills these talented interns were able move up to more sophisticated work for the company such as laser micromachining. The collaboration also allows Potomac to take macro scale work that they would not have taken otherwise since it’s not in their core business model of medical device and Biotech applications. Staff that Potomac hired such as Mollye Bendell, bring a level of creative design that also opened up some new digital fabrication projects. The City of Annapolis Maryland for example had Potomac laser mark sailboat-shaped bike racks with designs Mollye created. She is now also going on to grad school at UMBC.
Mike points out that the paid interns bring Digital Fabrication skills such as working with CAD, setting up lasers or other pieces of machines, and problem-solving. They are independent when they first start, and he adds they have an amazing work ethic. Ken finds that since the interns are earning money, they are also happier and have a better attitude since they feel valued.
Ken has found that in addition to additional revenue, the Intern program builds workers who are now readily employable given the skills they learned at Potomac such as quality control. Of course, Potomac is one of the first to snap up FLB interns and bring them in as full time staff. Our new night shift manager is a woman who started as a part-time intern.
The partnership with FLB has reaped more benefit for both parties than we could have hoped. It is yet another example of Potomac’s commitment to the local community that also strengthens our company and provides customers with the highest level of customer service.