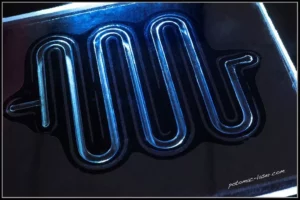
Potomac is continually developing new capabilities in order to give our customers the best solution for tough micro manufacturing problems. Driven by customer requests, our senior technical lead Natalia Christensen has developed novel laser welding processes for plastics that expands fabrication options when joining microfluidic devices, medical devices and other small products.
Laser welding of metals has been standard practice for many years especially in the automotive industry. However, plastic’s unique material properties have made the joining process more challenging. Ms. Christensen’s extensive R&D in collaboration with our customers now brings a sophisticated advanced manufacturing tool to the factory floor.
The Potomac laser welding process joins two plastic parts using a combination of heat produced by a laser and pressure provided by a clamping fixture. At this point our laser welding is only possible for thermoplastics such as acrylic, polystyrene, polyester, COC, or polycarbonate however these are important materials used in medical device, microfluidic, biotech, consumer and many other products. Welding similar plastics gives the best result, but some combinations of dissimilar materials may be possible. The material suitability for welding may also be impacted by additives in the plastic or special surface treatments.
Potomac can weld black to clear plastics: the top layer is transparent to the laser light while the bottom layer is absorptive. As a result, the laser beam melts the bottom layer and the heat is transferred then to the clear part, resulting in the interface between the two pieces melting together. The quality and strength of the weld depend on several factors, including laser power, speed, clamping pressure and uniformity, part design, etc. which we are able to optimize for best results.
The weld seam width typically ranges from 0.5 mm to 1 mm with variations caused by part geometry, application and materials. Dimensions outside these guidelines might be possible but testing is required for the particular design in a specific application.
Explains, Ms. Christensen: “Laser welding is a good alternative to bonding when adhesives are not desirable. For example, it can be challenging to contain the flow of liquid adhesives to specific locations on the part or in the case of medical devices, the chemistry might be toxic to cells. In many applications we can create a stronger bond than with other methods.” She adds, “most customers want testing of the laser welding results and so we have also developed pressure and flow tests to provide a complete service to our customers. With our long history of building equipment, we are able to build tools specific for product testing.”
With our extensive experience handling small parts and producing miniature feature sizes, Potomac is able to bring laser welding to our extensive micro-fabrication toolbox.