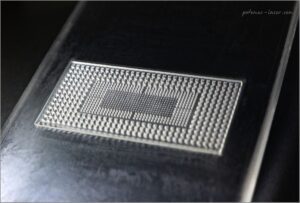
In the ever-evolving realm of microfluidics, the pivot from traditional materials to advanced alternatives is becoming increasingly evident. These “labs-on-a-chip” devices, pivotal in biological research, diagnostics, and drug delivery, owe their efficacy to the careful selection of materials and manufacturing methodologies.
Historically, Polydimethylsiloxane (PDMS) has dominated the microfluidic landscape. Its biocompatibility, flexibility, and innate transparency made it particularly suited for cell culture studies and academic pursuits. However, with the burgeoning demands of the industry, particularly in terms of manufacturability and scalability, the limitations of PDMS begin to surface.
Enter thermoplastics: materials that might redefine the future of microfluidics. Polymethylmethacrylate (PMMA) and Cyclic Olefin Copolymer (COC) are leading the charge in this transition. PMMA’s inherent transparency combined with its structural resilience, and COC’s remarkable chemical resistance and low water absorption, position them as frontrunners for microfluidic applications. A key advantage? Their compatibility with advanced manufacturing techniques, notably injection molding, which is tailored for large-scale device production.
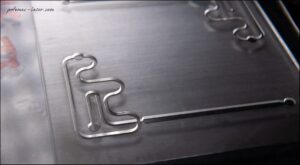
The transition from PDMS to thermoplastics isn’t just a leap in material choice; it’s a stride towards scalability and cost-effectiveness. Injection molding, a stalwart in thermoplastic production, outpaces the soft lithography of PDMS in efficiency and scale, offering rapid, high-volume production at a reduced cost-per-unit. This streamlined production not only caters to scalability but also effectively minimizes overall production expenses. The consistent nature of thermoplastics in mass production further trims down costs by reducing device rejection rates.
Potomac, recognizing these industry shifts, stands ready to aid customers in this crucial transition from PDMS to thermoplastics. Our deep-seated expertise in microfluidics ensures that while transitioning, the core functionality of the devices remains uncompromised. Additionally, their manufacturability receives a significant boost. Armed with a comprehensive understanding of both design and production prerequisites, our commitment remains unwavering: to drive microfluidic innovations to unparalleled heights