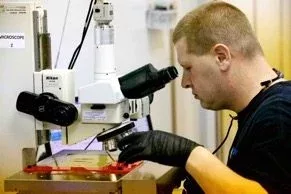
With each New Year come resolutions, and for Potomac that means incorporating more tools and techniques to help our customers achieve their goals. Here are some of the specific 2018 programs we’re putting in place for the medical device, biotech, microelectronics, microfluidics, R&D, consumer product and pharmaceutical markets.
Potomac’s primary emphasis in 2018 will be helping customers achieve faster time to market. Iterative rapid prototyping allows our customers to optimize designs so that products have a higher chance of success when they hit the marketplace. With our digital CAD files, customers can specify a part, test the prototype and if changes are needed, then modifications are quick and easy. But Potomac President and CEO Mike Adelstein points out that to support customers, the company must be positioned to quickly and economically execute. The ability to move quickly is especially important in going from rapid prototyping to production. Mike says, “Since Potomac has extensive experience as system integrators, we can easily build fixtures and customize our machines so that they are dedicated to production jobs.” Recently, Potomac worked closely with a large medical device company and in 60 days we were able to verify the process and move to production of 50,000 parts per month.
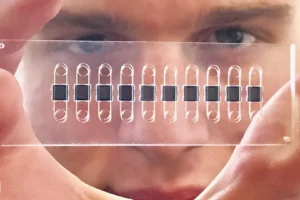
Potomac maintains an in-house toolbox giving us the best processing options for each micro manufacturing job. This year, Potomac is adding an intern from the University of Maryland, Baltimore County to help expand the 3D Printing Lab. Since 3D Printers are becoming more reliable, the additive manufacturing machines are now viable tools on the factory floor. With the ability to 3D print functional prototypes, the new machines will expand our rapid prototyping capabilities and allow us to explore the digital fabrication envelope.
Early research welding plastics has yielded significant results. In 2018, we will be designing a customized, dedicated machine for this technique which expands our work manufacturing plastic parts for medical devices and microfluidics. New plastics such as COC and PMMA compete with glass’ parameters at a fraction of both the purchase and processing cost making them a solid choice for many applications.
Laser micromachining is, of course, the heart of Potomac. Over the years we have increased the types of lasers in our factory beyond Excimer and can handle a wide range of materials. We will continue to develop micro CNC machining, bonding, stamping and other processes that speed time to market and add tools that increase our efficiency and productivity.
But at the end of the day, all of our tools and technologies, expertise and processes are only there to serve our customers. We expect to do just that in 2018.