Having the chance to improve safety of large industrial systems is a gratifying application in our digital fabrication work. One such application recently presented itself to Potomac through the University of Oklahoma’s [OU] School of Aerospace and Mechanical Engineering.
Growing out of a prime geographic location in the oil industry, the University of Oklahoma conducts a great deal of research on improving performance and safety for gas and oil drilling rigs. As we know from news stories any time a catastrophe hits, an oil well blowout is the uncontrolled release of either crude oil or natural gas due to failures in pressure control systems. Not only are the explosions from a blowout dangerous to workers who are often injured or killed, an accidental spark during a blowout can lead to a catastrophic oil or gas fire. And of course, there is the widespread environmental impact blowouts can have on the earth and its plant and animal life.
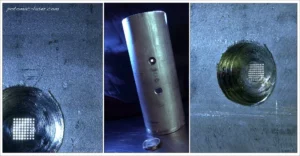
In their Capstone Senior project, a group of OU mechanical engineering students are studying ways to eliminate damage to O-rings in oil and gas equipment. It seems that O-rings can experience damage when they move across high-pressure ports. Currently the high-pressure ports, with diameters of 0.093 inches, are fully drilled. In order to mitigate the damage, the students have devised a solution by partially drilling the port to a specified depth, then allowing Potomac to laser drill holes of into the countersink to a depth 0.020 inches. Two different patterns of 100 and 200 microns in diameter could be tested for optimal results in keeping the O-ring in contact with the pipe as it passes over the pressure ports while still allowing fluid to flow through the port.
These dimensions pushed the limits of the school’s internal machine shop. So team member Taylor Lunger found Potomac through another group at OU that had had good success with our work. He comments that “small hole size was key to our project’s success, and Potomac was able to meet or exceed our parameters. In addition, we needed strong repeatability to ensure accurate test results.”
Hopefully, the OU studies will yield improvements in oil and gas well technology, thanks to innovation from engineering students and digital fabrication expertise from Potomac.