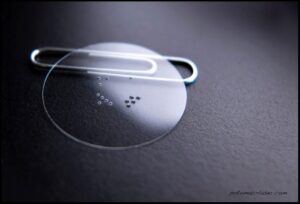
Perhaps the greatest benefit to being a graduate student is the opportunity to work with faculty who are conducting innovative research at the forefront of their fields. Biomedical engineering Ph.D. candidate Christos Michas is doubly fortunate since his area of study at Boston University [BU] combines the micro-scale 3D printing work of physicist Alice White who Chairs the BU Mechanical Engineering Department with the Tissue Microfabrication Lab research led by biomedical engineer Christopher Chen.
Professor White’s groundbreaking research in 2-photon Direct Laser Writing has led her to utilization of Nanoscribe 3D Printers to create small platforms that can be used in microfluidic devices. Michas is working to bring the new additive manufacturing platforms to the Chen lab’s work modeling vascular behavior in order to compare diseased to healthy blood supply systems. Understanding fundamental mechanisms are imperative for treating a wide range of diseases.
The research will also impact bio-printing organs. While researchers have successfully 3D Printed various types of human tissue, some tissue is difficult to vascularize. Without a consistent blood supply, tissue, and consequently, organs die.

Microfluidic devices can be complex structures, requiring integration of multiple tiny parts made of dissimilar materials. Because these small “labs on a chip” utilize small amounts of fluid, bonds must not allow any leakage.
In this project, Michas 3D Printed pipes with diameters in the 100 to 200 micron range that need to be connected to the microfluidic device. The design of the structure dictated that special glass substrates be manufactured with 250-micron diameter holes accurately placed to anchor the tiny pipes.
“With the high level of precision,” explains Michas, “we knew we needed to outsource the fabrication in order to guarantee the tight specifications. Potomac was able to meet all our requirements and the parts performed just as we expected.”
With its brittle nature, cracking and even shattering is an issue when trying to machine glass. The problem is exacerbated when working on such small spatial scales. Potomac has incorporated special techniques into their laser micromachining processes to ensure there is no damage to the material during or after the parts are manufactured.
This is a particularly interesting microfluidics project as it integrates advanced manufacturing tools in fabricating the device. 3D Printing brings a unique capability that works in concert with subtractive technologies like laser micromachining. As Potomac’s President and CEO Mike Adelstein likes to say, “Additive manufacturing is an innovative addition to our manufacturing toolbox, allowing us to choose the best tool for any digital manufacturing job.”