Inherent to Digital Fabrication is the ability to change a design quickly and easily in a Computer Aided Design [CAD] file. Need to modify a design for a part to fit a new assembly? Need to custom fit each customer? Need to change sizes from batch to batch? Piece of cake if you’re 3D Printing! Design changes are instantaneous in CAD files, opening up an entire new way to think about manufacturing.
In an age when customers want personalized lattes, hamburgers and clothing, mass customization is important for advancing the next industrial revolution. But beyond style and the cool factor, mass customization can actually aid form and function in practical ways. This is especially true in health fields.
Many people don’t realize that the clear Invisalign dental braces are actually 3D Printed using 3D Systems Corporation production printers. They are the same type of printer we have from 3D Systems here at Potomac. Orthodontists transfer their patients’ brace design to the San Jose based company, and overnight braces customized to each patient’s mouth are 3D Printed and quickly returned to the dentist. 3D Printing improves turnaround and creates optimal results for each patient.
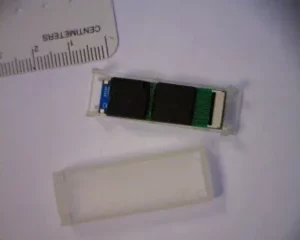
Kegan Fisher, the former Shapways Director of Industrial Engineering and Operations, recently founded Sols, a start up that promises shoes that fit each person perfectly. Says Ms. Fisher on her blog: Shoes that fit. Orthotics that are beautiful. Comfort + fashion. I never subscribed to the belief that beautiful couldn’t also be healthy. Sols joins Bespoke Innovations that 3D Prints custom prosthetics. Not only do they fit each patient perfectly to reduce discomfort, medical skin conditions and fatigue, Bespoke adds personalized colors and designs to give patients a fashion accessory instead of a medical device.
At Potomac we often work with medical device companies who are in the midst of clinical trials or FDA approvals. Creating a batch of say 100 or 1000 parts enables our customers to try a design and then modify it with a simple CAD change. We also 3D Print small batches of sensor and microelectronic parts.
Our partner, Potomac Meso utilizes our 3D Systems ProJet 3000 Plus machine to manufacture enclosures for micro-wireless sensors. Company founder, Dr. Paul Christensen, says the application makes sense for two reasons. “First, 3D printing is pretty inexpensive because of our small part size. And secondly, we build custom a variety of products that don’t lend themselves to very high volumes.” You can read the complete story here.
So if you have an idea for a customized product or only need small batches of parts, 3D Printing just might be the best solution for your manufacturing needs.