Part II of a series of blog posts focused on Innovative Manufacturing….
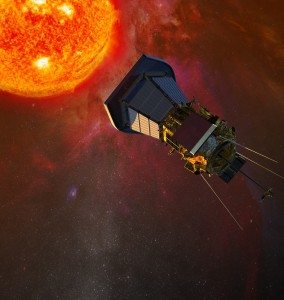
Micro marking is more than just being able to focus a laser to a small spot size. Accurate placement of marks on small components with high precision requires expertise in motion control, parts handling, and laser/material interaction. Potomac merged all of these capabilities in a recent project for NASA.
Solar Probe Plus, is an historic space mission from NASA and the Johns Hopkins University Applied Physics Lab (APL), to explore what is arguably the last region of the solar system to be visited by a spacecraft, the Sun’s outer atmosphere, or corona, as it extends out into space. NASA says “Solar Probe Plus will repeatedly sample the near-Sun environment, revolutionizing our knowledge and understanding of coronal heating and of the origin and evolution of the solar wind and answering critical questions in heliophysics that have been ranked as top priorities for decades. Moreover, by making direct, in-situ measurements of the region where some of the most hazardous solar energetic particles are energized, Solar Probe Plus will make a fundamental contribution to our ability to characterize and forecast the radiation environment in which future space explorers will work and live.”
Working so close to the dangerous surface of our closest star put extreme demands on the already tight specifications in space exploration. NASA needed to micro mark miniature custom connectors that are then attached to silicon detectors for the probe in an extremely small area. Characters could not be larger than 2mm. NASA engineers found that stenciling methods and silk screening procedures could not meet their stringent marking requirements. Laser micro marking seemed like the only solution and NASA found Potomac.
With the Potomac facility located only 20 minutes from the NASA Goddard Space Flight Center in Greenbelt, Maryland, we were able to work especially closely with the NASA team. After reviewing the project’s requirements, we agreed on a solution that would utilize a solid-state laser system that we built in-house, equipped with extremely precise motion control equipment.
Time was of the essence for NASA and Potomac was able to develop a process to mark the connectors less than a week after receiving the parts. With solid-state laser technology and state of the art precision motion control we were able to exceed the requirements for the project. The contrast was excellent and placement accuracy was verified using a NIST traceable vision system. After NASA qualified the parts and gave the approval to move forward, we ran the first two production batches to glowing reviews.
At the end of the day, we’re always happy at Potomac when we can help customers meet their goals and get exactly the parts they need. But it’s especially rewarding when we can also push the boundaries of space and science exploration.