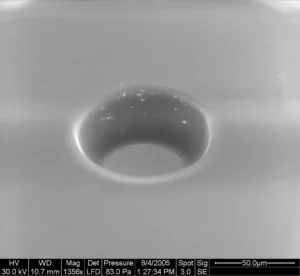
At Potomac innovation is not just another buzzword. Everyone, from our engineers to the operators on the shop floor, is continually looking for new ways to push the limits of standard laser micromachining technology. Almost perfectly smooth parts have been one of the manufacturing technology quests Potomac has successfully conquered through in-house manufacturing process innovation.
Our unique ability to drill holes or cut lines and features with very smooth surfaces is another reason to choose laser micromachining. Many processes leave behind rough walls or even burrs that are unacceptable, especially when building products at such small spatial scales. Burrs and other defects that might break off are especially dangerous for patients receiving implantable medical devices. You can also imagine catheters or other polymer-based parts being damaged as they are threaded through holes with rough surfaces. For these reasons, our customers demand the best finishes and we have solutions!
Heat Affected Zone
Manufacturing tools that generate heat create a change in the physical properties of the material being processed called the Heat Affected Zone [HAZ]. This may just show up as a discoloration but often if high enough temperatures are reached the area will actually melt and recast or reform into rough, extraneous material.
At Potomac, we’ve actually built lasers and so have a unique set of skills to optimize laser performance. Adjusting the fundamental laser parameters in the wide range of laser tools we use from infrared to ultraviolet, allows us to drill holes or cut features that have inherently smooth surface finish.
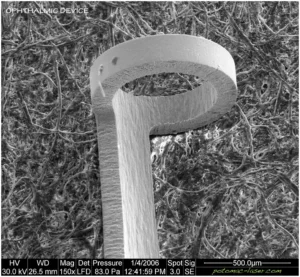
Laser micromachining utilizing ultraviolet [UV] laser wavelengths between 355 and 193 nm is primarily a photo-ablative rather than a thermal process. When a material absorbs UV photons, covalent bonds are broken and the material literally flies apart. To be technically correct, there is a secondary thermal process but by the time it happens the UV laser beam has usually moved onto the next area.
The HAZ also increases the risk of cracking in metals, glass and ceramics. Imperfections in the composition of the material literally open up the part to increased fatigue or stress, and cracks may form. Potomac’s ability to create parts with little or no HAZ not only yields great surface finish; we create a stronger, more robust part.
In some instances, ablated material will fall back to the work surface and re-attach, especially when the particulates are very small. To avoid this, an assist gas is often used to blow the ablated material away and keep the work surface clean. When working with long wavelength laser light in the infrared, if heat does generate any minimal recast, Potomac has developed sophisticated post-processing methods that yield smooth parts in materials such as metals.
Additionally, because laser light is a non-contact process, the surface of a hole or cut will not have the ridges mechanical tools make as they move along a substrate. Even 3D Printing at its lower resolution settings will have a rough surface where you can see the layers being set down.
Polymers and Organics
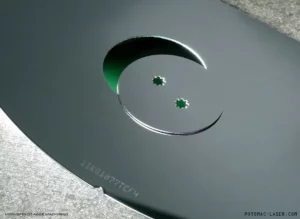
UV light at 248 and 193 nm is strongly absorbed by polymers and organic materials and usually leaves behind no HAZ. This is why the excimer laser was the tool of choice for LASIK eye surgery. The fine precision cutting required to re-shape the cornea has no room for any thermal damage. For these materials that are commonly used in biotech and medical device manufacturing, we also have the short wavelength lasers to make medical grade parts of exceptional quality.
For drilling small holes or making features in small parts, Potomac’s innovative laser micromachining technologies can produce almost optically smooth surfaces in a variety of polymers, glass, ceramics, metals, silicon, quartz and diamond. If other factors such as size, aspect ratio, and material make sense, Potomac’s innovative laser micromachining is the best choice to avoid HAZ, creating small holes, cuts and features with beautiful surface finish.