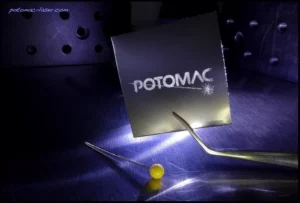
Part I of a series of blogs posts focused on Innovative Manufacturing Technologies
As the trend toward miniaturization of devices accelerates, finding the right tool for the job is becoming more challenging. Options that initially seem promising often fall short of expectations because they cannot meet tolerances, are not cost effective or have the ability to ramp up for production. Innovation, creativity, and communication are often the difference between achieving success or going back to the drawing board.
Our mission at Potomac is to help our customers navigate these obstacles in order to find the perfect solution to their manufacturing requirements. In planning, a significant amount of time is dedicated toward discussing the technical requirements of the project, others areas such as short and long terms goals, volume requirements and cost targets are also discussed.
Case Study: Backlighting Application
As simple as it may sound, backlighting in the micro world can be a little tricky. To provide a sleek, clean, technological look, manufacturers want to have seemingly unmarked opaque materials allow light to pass through them for the purpose of revealing graphics, logos, or indicators. How is this bit of illusion achieved? Well, micro holes of course! These holes can be as small as a few microns and can number in the thousands. Imagine a blank panel suddenly becoming a work of art or something as mundane as a light switch with setting indicators appearing as they are activated.
Potomac was recently contacted by a customer to drill a pattern of holes in the shape of a tractor trailer for the purpose of testing a backlighting application. They wanted 200,000 holes with 10 micron diameters through metal that was 50 microns thick. To aid the effect, they wanted the holes as tightly spaced as possible.
So, considering these requirements, the next step was to determine the best tool for the job. 3D Printer? Amidst all of the media buzz, it just cant accomplish these feature sizes…yet. Micro-CNC? While there are those who make 5-10 micron bits (that we can’t see), this technology would not provide the speed, and the bits would likely wind up breaking with enough frequency to be a hindrance. Laser? Ahhh yes, speed, feature sizes down to 1 micron, proven technology, and cost-effective.
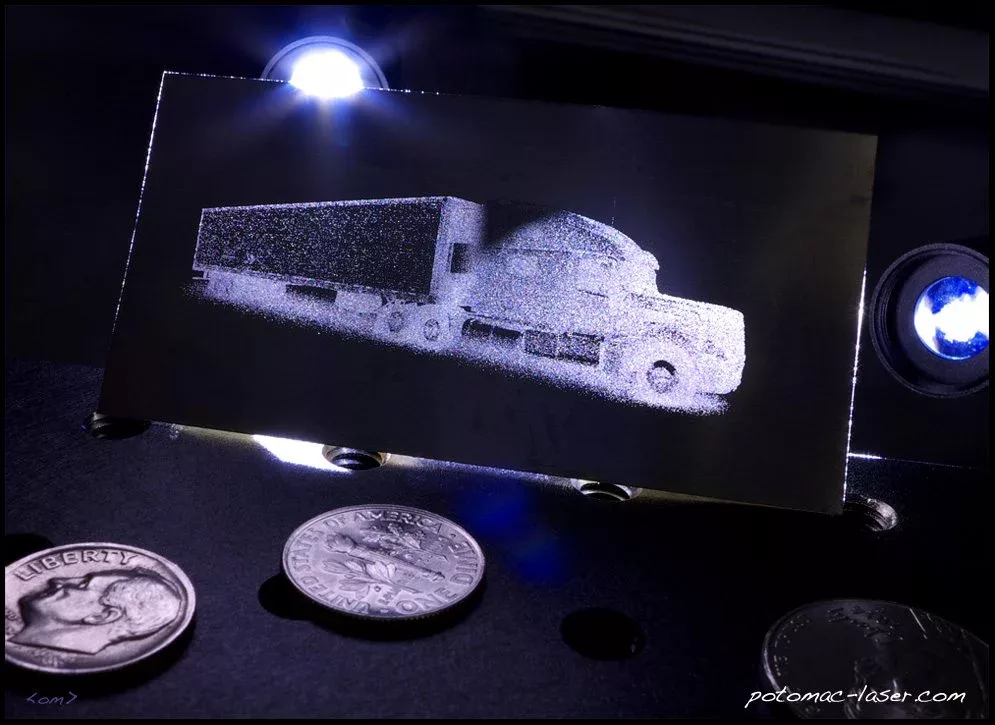
With the laser being the tool of choice, all that was left was to make it work. First challenge was how close can we space the holes. Spacing had to be close enough to maximize the backlight effect, while leaving enough material between the holes to retain the structural integrity of the substrate. Factors to consider are the fact the laser drilling leaves a tapered cut, along with any thermal effects. Ultimately, we settled on 50 micron hole-to-hole spacing with holes that were 10 microns on the exit side with 12-13 micron entrances.
To help offset some of the thermal effects caused by the laser, tight hole spacing, and the hole density, which could result in material distortion and ruin the illusion, the metal of choice was tantalum. Stainless steel, on the other hand, tends to warp when processed under similar conditions.
As the process was being planned, it was determined that less attention needed to be directed to how perfect the holes appeared. Instead, the holes just needed to be open to allow the light through. So, slight variations in hole size and shape were to be disregarded, provided all of the holes were open.
Game Day: While lacking a frozen tundra, the gameplan still had to be executed. Having selected the most appropriate laser wavelength, determined the most suitable material, and agreed upon the acceptable hole parameters, it was time to bring it all together. The laser system was equipped with optics that allowed for the production of 1000’s of 10um holes per minute. So, once the hole size was dialed in and the cut quality was deemed acceptable, things were turned over to the QC team. Under further review, there were no penalties and play could commence. The light show was initiated and the results were glowing!
Overall, this was a fairly straightforward project, but backlighting is an exciting new application that is gaining momentum and finding its way into many industries. In the coming weeks, we look forward to sharing our micromachining odyssey with you as we move to change the world one micron at a time via imagination, innovation, and inspiration.