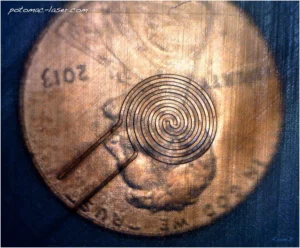
At Potomac Photonics, we often talk about the importance of using the right tool for a specific job. Whether it’s 3D Printing, laser processing, Micro-CNC, or any other technology, we have expertise in multiple processes. Often, we combine more than one to get the best solution to our customer’s tough manufacturing problems. By adding hot embossing to our Digital Fabrication toolbox, Potomac is now able to combine this powerful replication technique with laser micro-machined masters to make high precision, high quality parts quickly and at a fraction of the cost of other methods.
There are a number of advantages to the Potomac system. First and foremost, laser micromachining can replace lithography in making the master. Laser micromachining can generate a master in as little as 24 hours which is a substantial improvement in delivery time. Further, Digital Fabrication from a customer drawing allows quick design change iterations and the ability to test new ideas quickly. With our UV laser processing we have the flexibility to create features as small as 5 microns with tight tolerances or substantially larger features to meet your specific microfluidic application needs, all with fast turnaround.
On the economic side, Potomac’s process can be accomplished at a fraction of the cost. Generating the master through laser micromachining is an order of magnitude less expensive than traditional processes. Of course, using one vendor for both creation of the master and the replication process also means savings in communication, time, and energy!
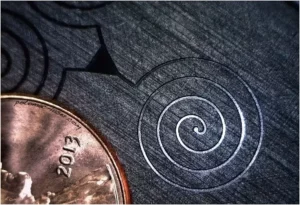
While these benefits are great for rapid prototyping, it’s important to note that the hot embossing step can stamp volume parts at once to produce quantities perfect for short production runs. Additionally, hot embossing allows us to create devices in materials such as polystyrene, PMMA and Cyclic Olefin Copolymers that can’t be easily machined either by lasers or micro-CNC.
Microfluidic devices are a great example of how Potomac can draw from a diverse Digital Fabrication Toolbox to complete the entire part. The field is seeing a move to polymers, as there are improved performance characteristics at a fraction of the cost over glass devices. Using laser micromachining we can fabricate a master, then hot emboss the design into plastic, and then bond glass covers onto the device for easier visual inspection while ensuring a good seal that can withstand pressure. If needed, we can also drill micro holes for fluid introduction. For added functionality, Potomac MesoSystems can add microelectronics interfaces for full integration into an assembly.
We’re excited to have new hot embossing capabilities in our Digital Fabrication Toolbox! So send us your ideas and see how we can give you a rapid, low-cost manufacturing option for your next project.